I was recently lucky enough to be asked to do a press check. Normally this would be a simple, even boring task – that I’d still be happy to perform for any client! – but I’ve found that things are rarely boring in the craft beer industry.
This press check was at the Ball Aluminum Manufacturing plant in Tampa, FL, where they make 8,000,000 cans over three shifts every day of the year except Thanksgiving and Christmas. This is just one of several manufacturing facilities they have around the country and it’s not the highest capacity!
Let me implore you now to please recycle those aluminum cans!
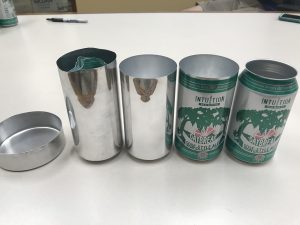
After the colors were dialed in on our newest can design we got a tour of the plant. The process by which that soda or beer can on your desk was made is staggering in its scale. It all starts as a gigantic roll of flat aluminum that’s punched into shape and imprinted while traveling through the floor and ceiling between machines.
It’s hard to explain this sort of volume, but in the 20 minutes that it took for us to tour the facility’s manufacturing line there were already pallets of our cans stacked and ready to ship out.
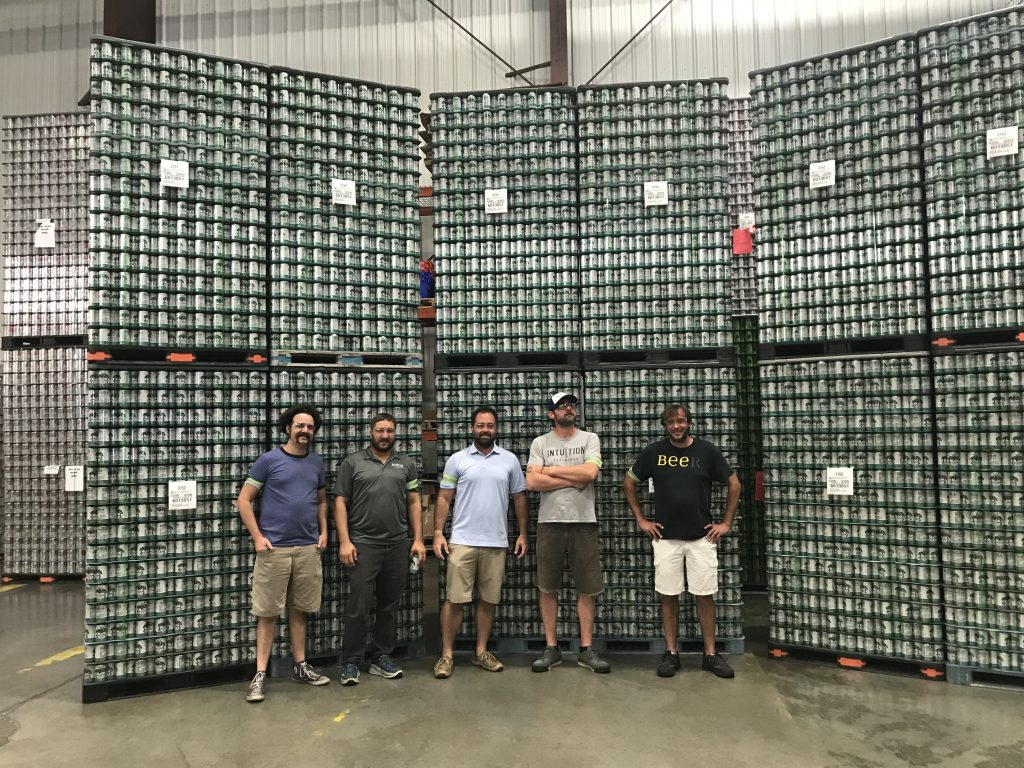
The holding area at the end of the production line looked like the warehouse that stores the Ark of the Covenant – just cans stacked from floor to ceiling! Now I’ve spent entirely too much time searching for a .gif of the final scene of Raiders of the Lost Ark, so I’ll just end by asking you to pick up a six-pack of Daybreak when you see it on the shelf.
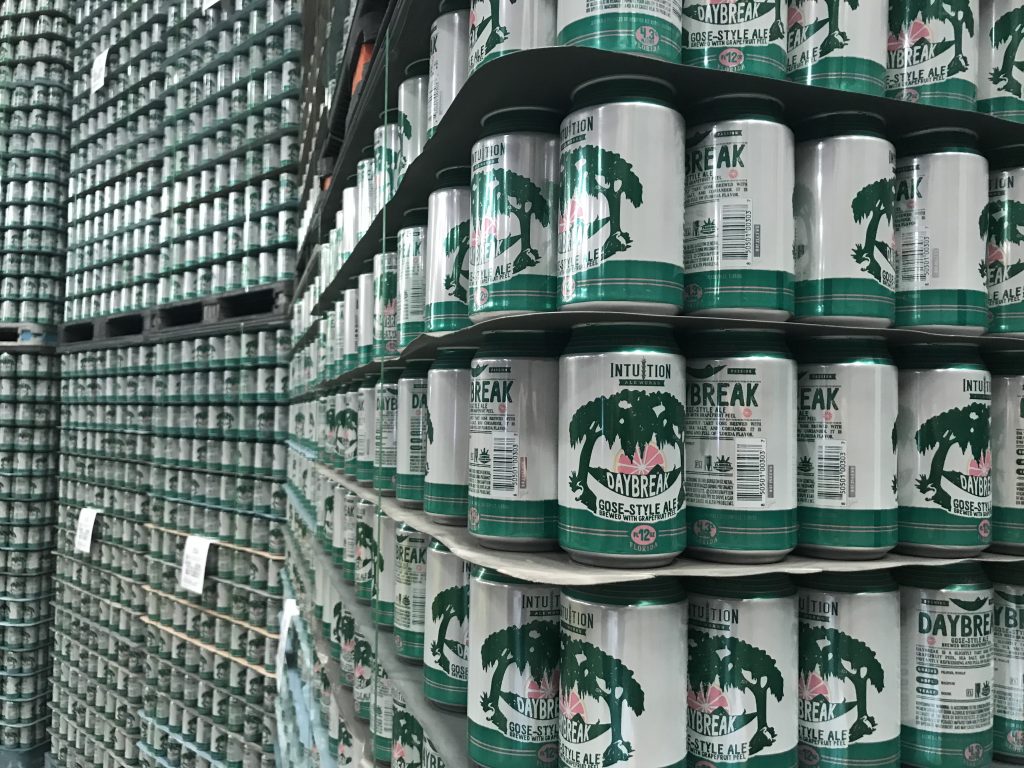
Everything is very open with a really clear clarification of the challenges. It was really informative. Your website is useful. Thanks for sharing!|
Pingback: Ride the Wave! – Cowford Creative Services